Tactile feedback, also known as haptic feedback, is a crucial element of modern human-machine interface (HMI) design. Whether you’re designing a keyboard, vehicle control panel, or industrial machinery, the way a button or switch “feels” can significantly impact usability and user satisfaction. Achieving optimal tactile feedback involves understanding various mechanisms and selecting the right solution for your application. APEM specializes in providing ergonomic, reliable tactile feedback solutions tailored to diverse industries and environments.
KEY QUESTIONS FOR CHOOSING THE RIGHT TACTILE FEEDBACK MECHANISM
Selecting the most relevant product for a project is sometimes difficult. The first step in getting the right feedback is asking the right questions:
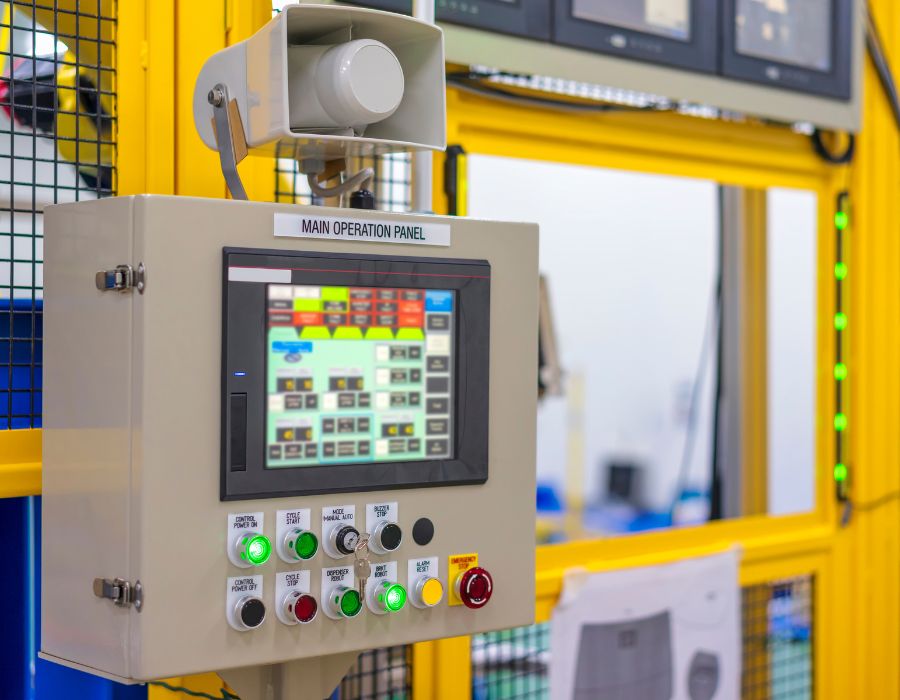
- Frequency of use: Will the switch be frequently or infrequently actuated?
- Signal clarity: How distinct should the actuation feedback be?
- Actuation strength: How much force and travel are needed?
- Environmental conditions: Will it be exposed to vibration or sealed against harsh environments?
- Durability and cost: What is the required lifecycle, and how budget-sensitive is the project?
THE PRINCIPLES OF TACTILE FEEDBACK MECHANISMS
Tactile feedback can be achieved via a spring mechanism, a metal dome or a polyester membrane. With all three materials, deforming the initial and preferred state of the device enables contact with a switch actuator.
But that’s where the similarity ends, and choosing between the options is a lot easier when you know the strong and weak points of each type. Tactile feedback mechanisms vary greatly as to cost, reliability and feel.
But perhaps most importantly, they require varying degrees of force and travel (pressure and distance) to engage the switch. These last two variables impact the life expectancy of the device and the ease of use for the end user. The tactile feedback of a computer keyboard switch, constantly in use and requiring little force, should not resemble that of a forklift safety switch, where gloved, infrequent use calls for significant resistance and a highly charged feedback.
APEM ENGINEERS’ GUIDE TO TACTILE FEEDBACK
Finding the perfect tactile feedback is as much about understanding the science as it is about knowing your application’s needs. APEM engineers have put together a practical guide to help you decode the nuances of tactile feedback mechanisms—giving you a clearer path to the ideal solution.
- SPRING MECHANISMS: A TALE OF VERSATILITY AND SUBTLETY
Spring-based mechanisms are the workhorse of tactile feedback, adaptable to a wide variety of applications like construction machinery or material handling. But the magic lies in their configuration—whether they’re vertically or horizontally positioned.
- Vertically positioned springs
These are your go-to choice for robust designs with frequent actuation. Designed to compress directly, they excel in durability, with lifespans that can reach an impressive 10 million cycles. While they handle long travel distances like a pro, they lack the satisfying “snap” that many users expect in tactile feedback. For applications prone to vibration, they might need a helping hand to avoid accidental actuation.
Best fit: Think keyboards, control panels, or switches where longevity matters more than distinct tactile feel.
APEM’S product:

IP – Momentary Pushbuttons
Designed for harsh environments, these IP67-sealed pushbuttons offer exceptional reliability, customizable options, and long-lasting performance.
- Horizontally positioned springs
Horizontally positioned, spring mechanisms have a distinct tactile feedback which is accompanied by a metallic clicking sound at the moment of actuation. These mechanisms hold up well in environments where they are subject to vibration or strong current.
Pair them with a membrane, and you’ve got the added bonus of an effective seal.
Best fit: Heavy-duty machinery, off-road equipment, or anywhere feedback clarity meets durability.
APEM’S product:
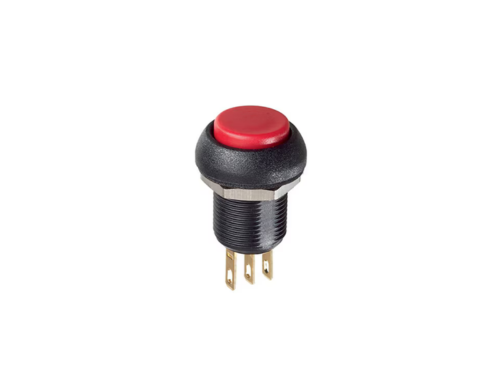
IM Pushbuttons
Engineered for harsh and noisy environments, the IM pushbuttons deliver strong, audible tactile feedback, ensuring reliable performance even under vibrations and shocks.
- METAL DOME MECHANISMS: THE MAESTRO OF PRECISION
Metal domes are formed out of stainless steel that, when compressed, collapses, actuates the switch, and then releases to its initial convex configuration. Metal domes provide a great deal of positive response, giving the user a crisp, precise activation signal.
They are, however, size limited: past 16mm, the metal cannot be reliably counted on to properly return to its initial configuration.
Metal domes provide superior tactile feedback and usually carry the highest price tag.
Best for: Compact devices where feedback clarity and precision are essential.
APEM’S product:
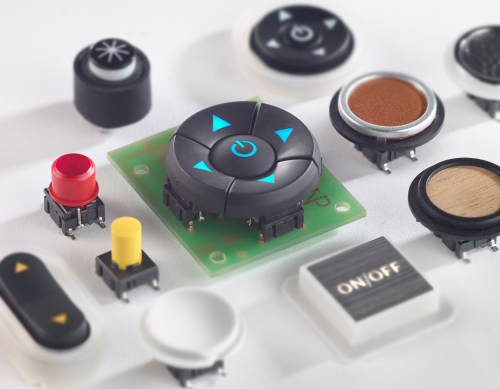
MEC switches
MEC switches provide exceptional tactile feedback and endless customization, with Unimec, Multimec, and Ultramec offering IP67 sealing, durability, and advanced navigation solutions for versatile HMI designs.
- MEMBRANE MECHANISMS: WHERE COMFORT MEETS ENDURANCE
In membranes, the inside of a polyester bubble is coated with graphite. Membranes can reliably function at larger sizes than metal domes and are typically less expensive. The feel of a membrane is less precise than metal, because the collapsing dome doesn’t provide as much positive response.
This can be advantageous in high repetition uses, where transmitting too much energy back to the user can be ergonomically disadvantageous. Although still size limited, membranes can be effective in larger sizes than metal domes and usually have a longer life span.
Membranes can be configured into virtually any shape, sealing the switch without additional components.
All tactile feedback devices need to be calibrated for the intended end use.
Best fit: High-repetition tools, large-format switches, and cost-conscious designs.
APEM’s product: Get more info about Membrane keyboards technology
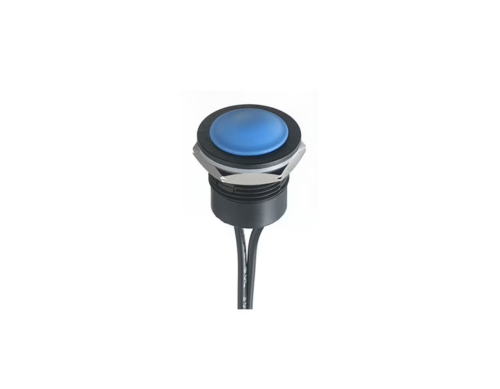
IA Pushbuttons
With a polyurethane membrane actuator and IP67 front sealing, IA pushbuttons combine tactile feedback with resistance to frost, sand, and hydrocarbons, ensuring smooth operation even in challenging environments.
FINE-TUNING TACTILE FEEDBACK
APEM ensures that all tactile feedback mechanisms are precisely calibrated for their intended applications. Using the Force Stroke Machine, each switch’s performance is tested and fine-tuned to provide the perfect balance of force, travel, and feedback, guaranteeing an optimal user experience.
This guide makes it easier to identify the right tactile feedback mechanism for your specific needs. Ready to design the perfect switch? Contact APEM’s experts today using our form and let us help you bring your project to life.