Human-machine interfaces (HMIs) are central to operating machinery. However, when working on construction sites, agricultural fields or military operations, it is crucial that your control panels are robust and sealed against environmental conditions, such as sand, mud, and dirt. This resistance is crucial to ensure durability, functionality and safety. Therefore, when choosing HMIs, you’ll face the question: How can I protect my HMIs effectively against corrosion from sand, mud and dirt?

What damage can sand, mud and dirt cause to your HMI?
Dust and sand particles are extremely small and don’t pose a serious threat at first. However, if millions of fine particles infiltrate the smallest cracks of your control panel, it will gradually block mechanisms and limit its functionality. The situation worsens when liquid mud flows through tiny cracks and connection points that are not fully sealed. When the mud dries up, it will get stuck, causing a complete shutdown of your controls in the worst case.
Moreover, the necessity for frequent cleaning to eliminate accumulated dirt can accelerate corrosion even further. This illustrates another aspect of why choosing robust and highly qualitative HMIs is substantial in this context.
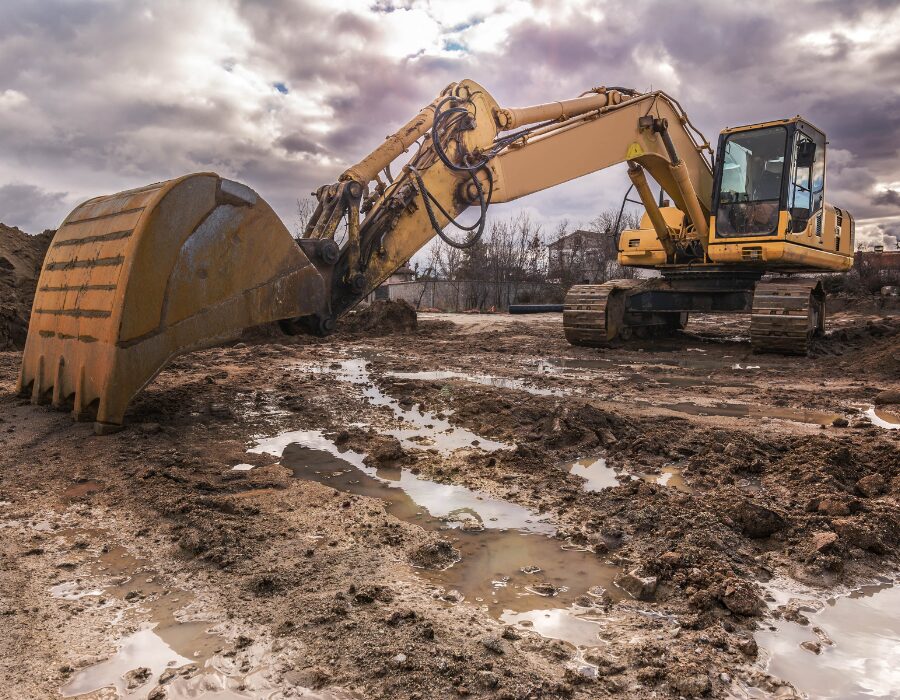
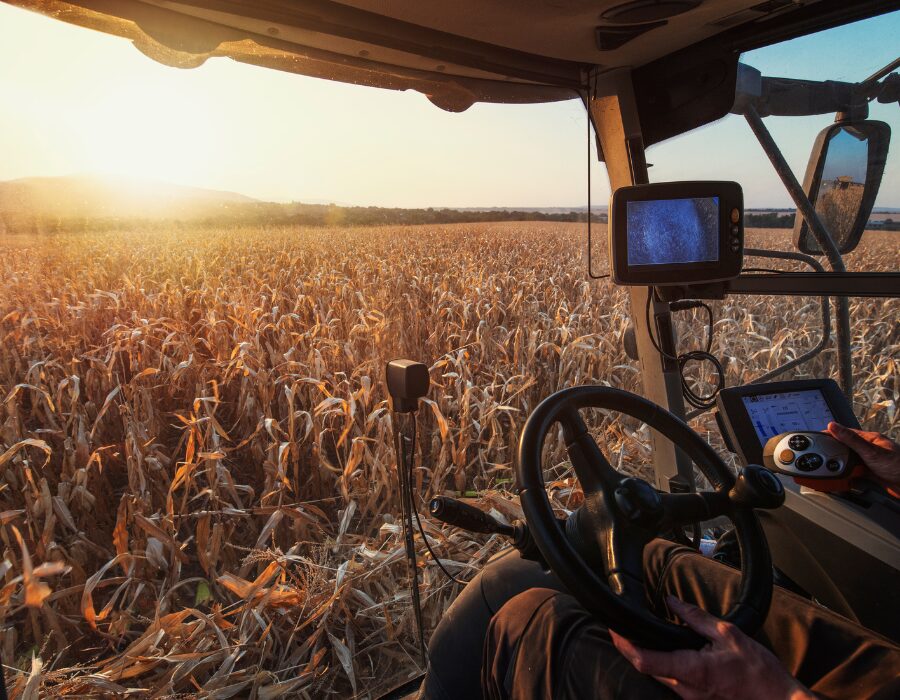
How do I design my HMI to resist environmental conditions?
To achieve effective designs for your HMIs to combat sand, mud and dirt exposure, strategic considerations are essential. Especially in the agriculture and construction market, manufacturers are tailoring their HMI design to includes easy-to-clean interfaces that reduce downtime and intuitive controls that enhance usability, even for operators wearing gloves. Additionally, the interface must facilitate easy access for cleaning and repairs.
Sealings and coatings offer robust protection. Special coatings are applied to rubber solutions, offering defense against UV light degradation, a common challenge in open-field settings. Elastomeric keyboards are an example of innovation in sealed solutions. Made from one seamless piece, they not only provide a natural seal once mounted but also embody the ruggedness required for harsh conditions. Furthermore, high mounting positions help evade ground-level challenges. Materials like stainless steel provide high durability and resistance to corrosion.
However, the goal is not only to create a sealed solution but also to engineer control panels, joysticks and switches that the user can trust and rely on. This is where Ingress Protection (IP) ratings come into play. Ratings such as IP67, IP68, and IP69 indicate water-resistant and waterproof capabilities that are essential for HMIs in demanding environments.
IP67 vs. IP68 vs. IP69: What is the difference?
The IP (Ingress Protection) rating is a standard that classifies the degrees of protection provided against the intrusion of solid objects, dust, accidental contact and water in electrical enclosures.
IP67 indicates that the device is protected against dust ingress and can be submerged in water up to 1 meter for 30 minutes. This level of protection is common in devices that might be exposed to water occasionally but not under high pressure or for extended periods.
IP68 builds on IP67 by offering a higher level of water protection. The specifics of IP68 can vary by manufacturer. The device can be submerged deeper than 1 meter, but the exact depth and duration are determined individually for each product. This rating is seen particularly in devices that are more rugged and water-resistant.
IP69 provides further protection against close-range high-pressure, high-temperature spray downs. This level of protection is typically more relevant to industrial equipment or medical devices, which requires rigorous cleaning processes or extreme conditions.
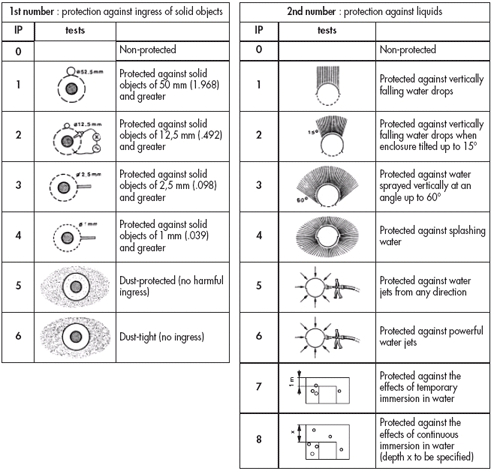
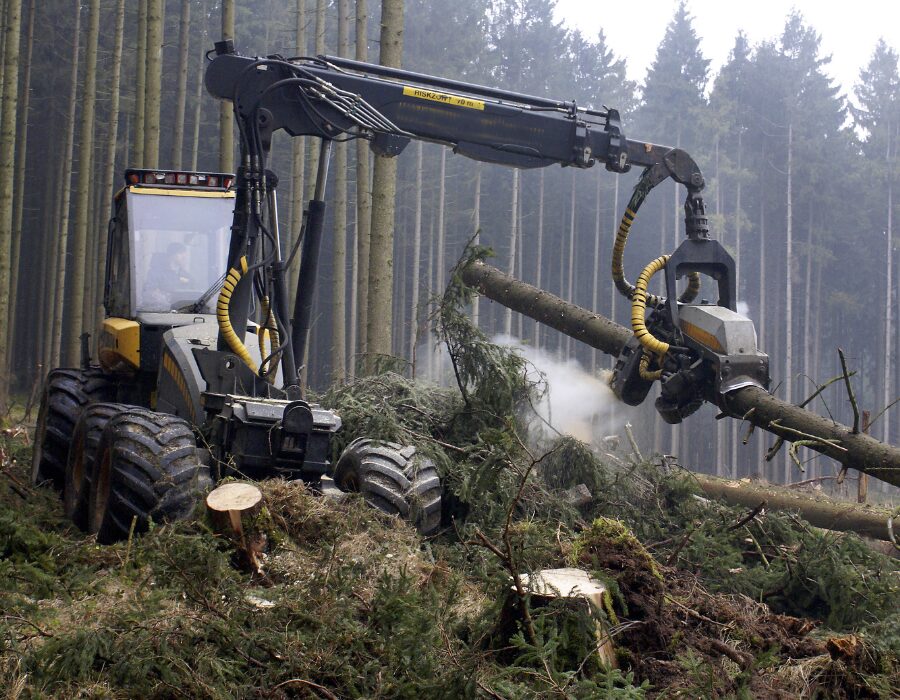
Main applications
- Agriculture
- Construction
- Mining
- Defense
- Vehicles
- Material handling
- Forestry
Excellent HMI solutions against sand, mud and dirt
The design of HMIs goes beyond mere resistance to sand, mud and dirt. It’s about creating interfaces that are resilient and enduring to use. With decades of experience in the construction, agriculture and defense industries, APEM has mastered the art of providing environmental protection solutions. We provide IP tested HMI solutions.