Last option on the safety chain: Emergency-Stop switches are one of those rare things like firefighters that you hope you never have to use. They are the safety solution for that unfortunate situation when everything else has failed.

WHY USE EMERGENCY-STOP BUTTONS?
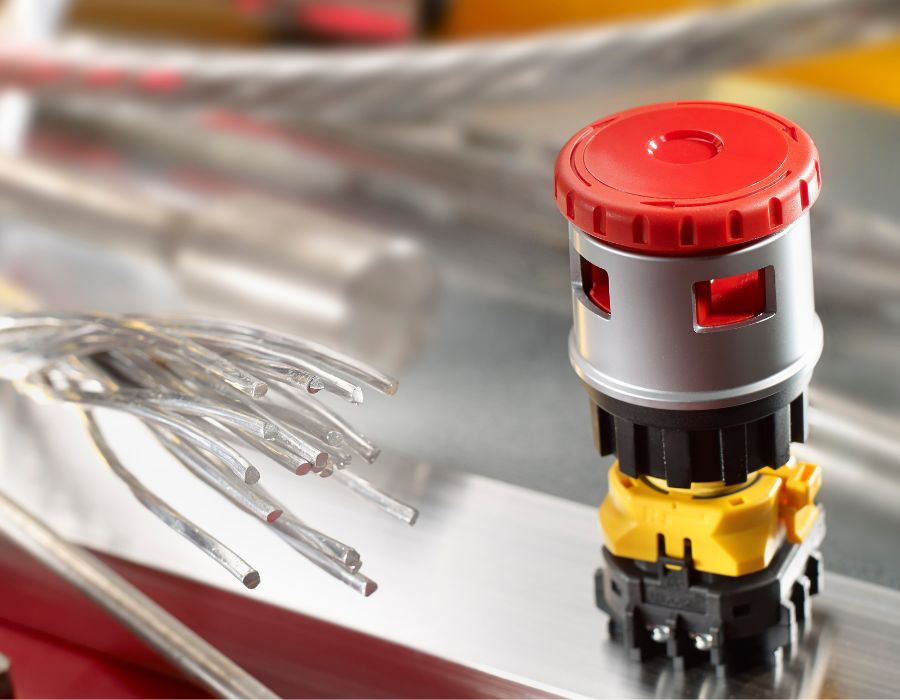
Ideally, the E-Stop button should never be activated. The machine designer should at first think of what can make the machine safer to use and maintain, in this order:
- Rethink and redesign the safety-critical parts of the machine
- Add mechanical solutions and protections to prevent access to the hazard
- If all the above are not enough, what electronic options are there?
- Last point and if possible what should be avoided – what PPE is required to operate this machine safely?
On top of all these steps comes the Emergency-Stop switch.
WHERE EMERGENCY-STOP BUTTONS ARE USED?
E-Stop buttons have become an everyday sight with their easily recognizable mushroom with a red top. They are everywhere – not just in industrial applications, like remote controls, belly boxes, AGVs and walkie pallet jacks, machine tools and production lines, but also in everyday life, for example on the escalator you take in shopping centers or the automatic door to your dentist.
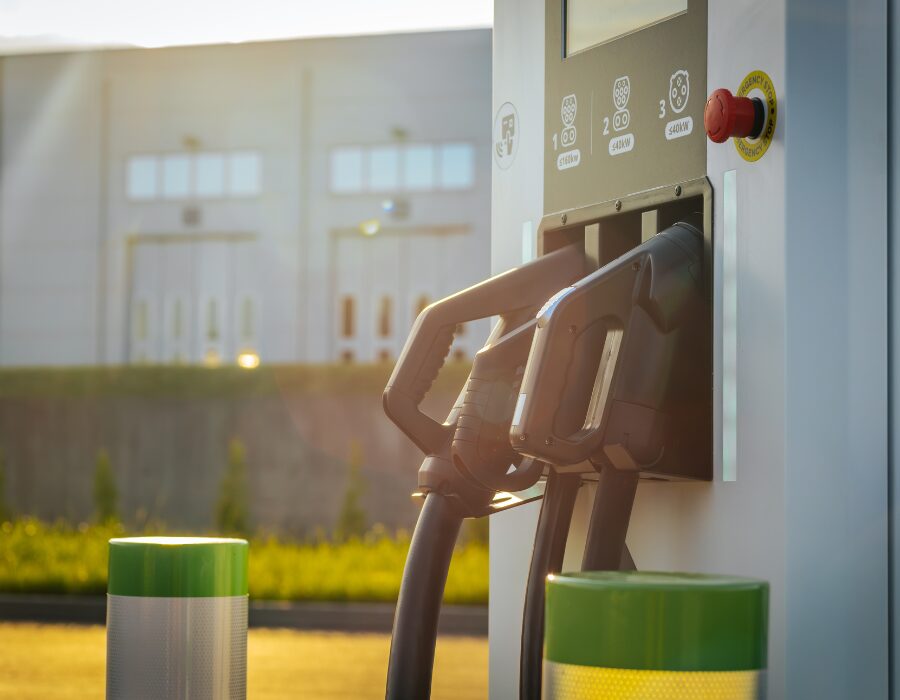
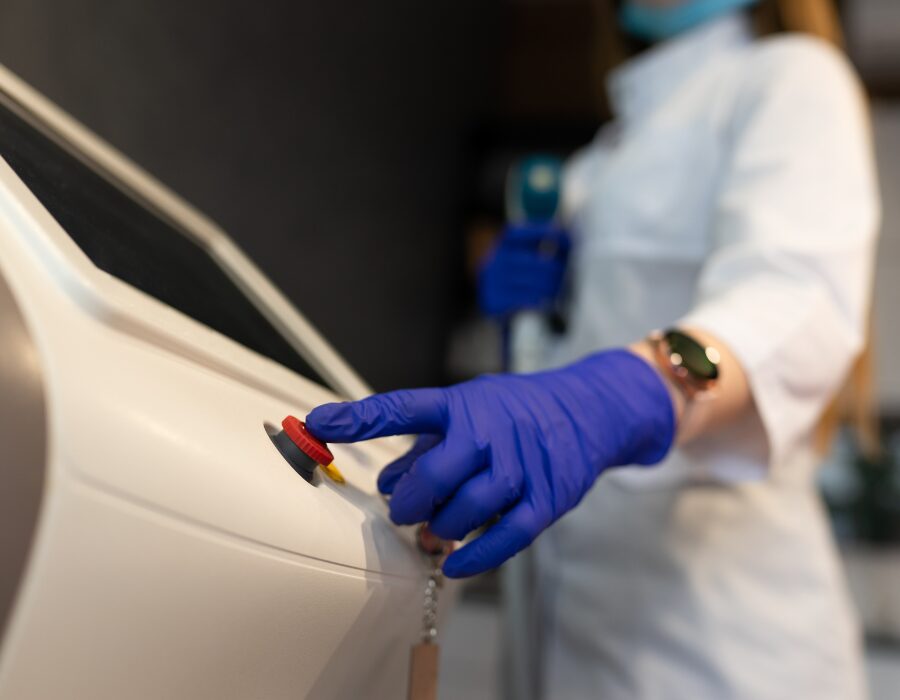
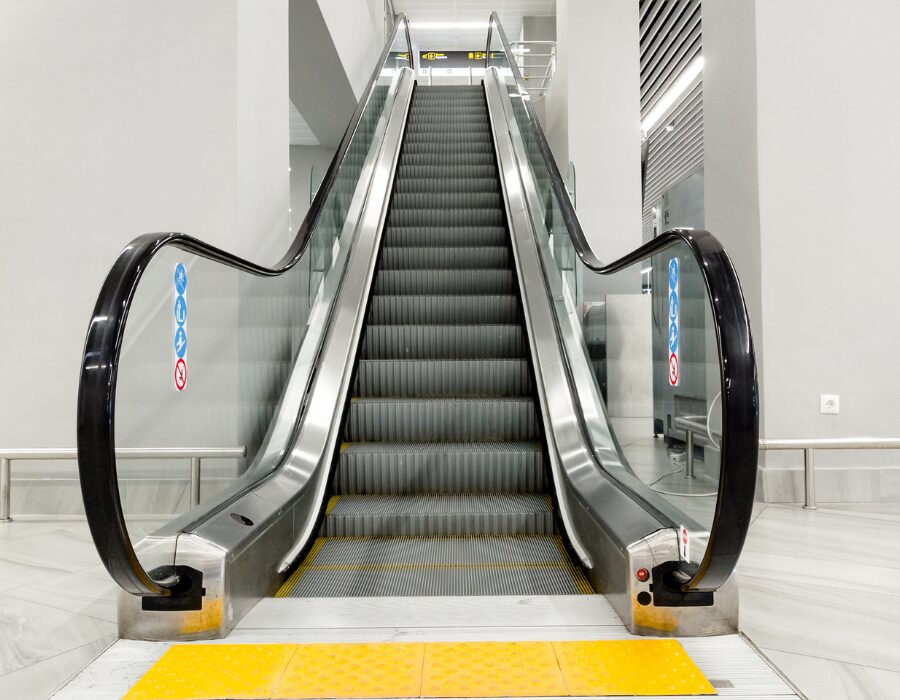
As technological development moves toward more and more electrical vehicles, the use of E-Stops will continue to expand. The requirements for Emergency-Stop switches depend very much on the application they are used on and the environment the machine is in.

DEMANDS ON RELIABILITY
Emergency-Stop switches have always needed to be reliable – the option of last resort must work, and it must not be mistaken with other functionalities. If it fails, it should be without threatening the safety of the workers around the machine. That is why the standards are evolving and new solutions are available on the market such as fail-safe options or self-monitored contacts for the most critical applications.

AMOUNT AND LOCATION OF EMERGENCY-STOP BUTTONS
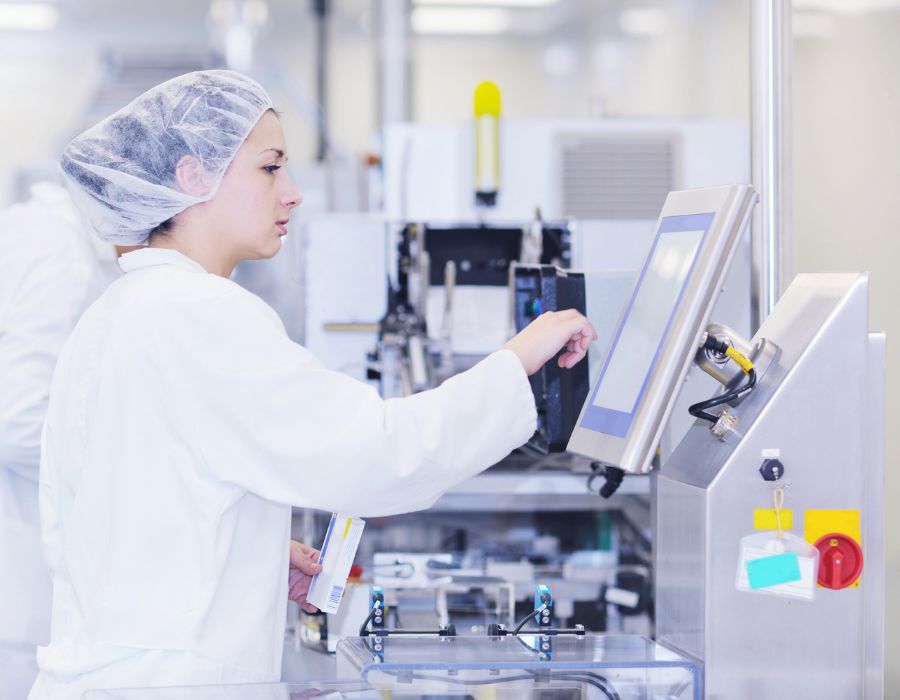
Whether on an automated production line, a construction vehicle, a medical device, or even an escalator in a shopping mall, determining the right number and placement of Emergency-Stop buttons is critical. The key questions remain the same:
- Where should the Emergency-Stop be installed?
- How many are needed?
- How do they communicate with each other?
- Which part of the system or machine does each E-Stop command?
In any application, from industrial systems to special vehicles or public infrastructure, the E-Stop must be easily accessible for immediate actuation—but also strategically positioned to avoid accidental activation. Ideally, it should allow a targeted stop without unnecessarily halting an entire system.
In remote control scenarios, complexity increases: is the E-Stop operational? And which subsystem will it deactivate? The rule of thumb: place the Emergency-Stop wherever the operator is expected to interact with or control the equipment—this includes fixed control stations, mobile HMIs, and vehicle-mounted interfaces.
SIZE AND COMPACT INTEGRATION
As devices are becoming smaller and Emergency-stop switches are required on remote controls, the size of the switch is increasingly more important – this includes both below the panel as well as the above panel height.
Because the E-stop should be located near the worker but not be too intrusive so it wouldn’t be activated by mistake, machine designers are looking for smaller devices. It should be easily reachable for the worker in an area already populated with many other controls.
Here are some options for Emergency-stop switches that fit these trends of compact size and demanding requirements for reliability.
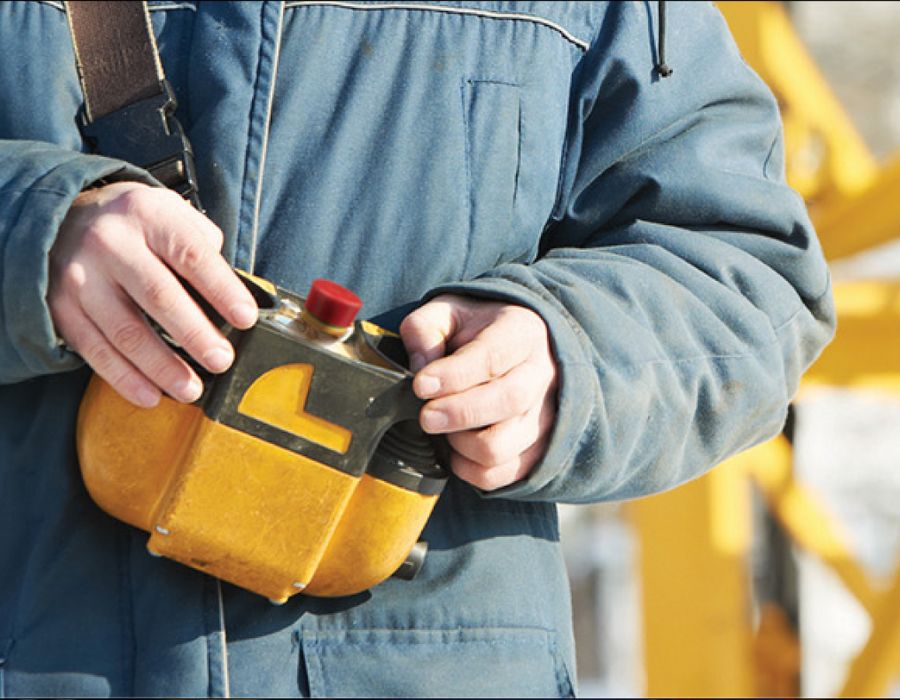
EXPLORE APEM’S EMERGENCY-STOP RANGE
Here are some options for Emergency-Stop switches that fit these trends of compact size and demanding requirements for reliability.
APEM’s E-Stop products are designed to meet the specific needs of industrial and mobile applications, including handheld HMIs, electric vehicles, and construction machinery.
We offer:
- Compact, low-profile designs
- High-reliability switching systems
- Ingress protection for demanding environments
- Compliant products with international standards like ISO 13850
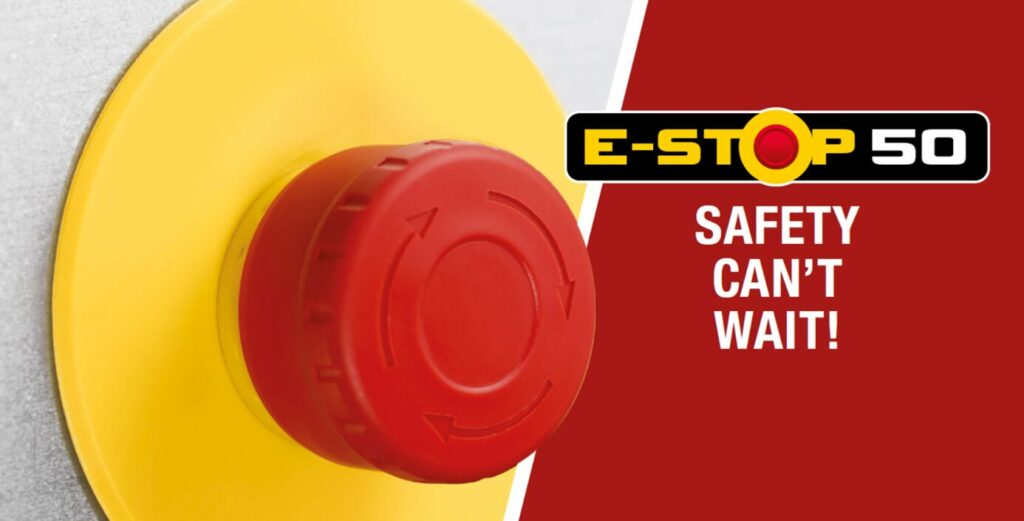
SAFETY CAN’T WAIT – E-STOP 50, SHIPPED IN 48 HOURS
E-Stop 50 is the ultimate selection of high-performance Emergency-Stop switches, developed by IDEC and APEM. All references are available ex-stock and dispatched within 48 hours* — ensuring no delay in securing your operations.
*Subject to availability and delivery zone.
IDEC EMERGENCY STOP SWITCHES:
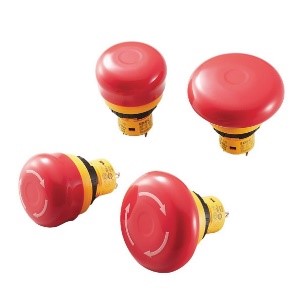
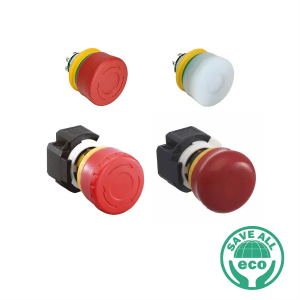

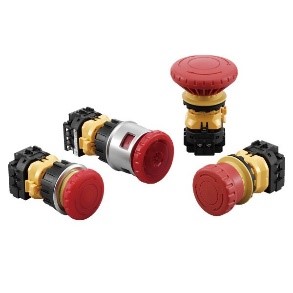