Joysticks are among the most versatile solutions in the designer’s toolbox. Joysticks are intuitive enough to be quickly mastered by new users, while their proportional response enables experienced operators to achieve remarkable levels of precision. This has led to the adoption of joystick controls for a wide range of demanding industrial applications. Commercial and heavy vehicles, as well as machine controls, all benefit from the versatility of joystick design.
“The longevity of Hall effect joysticks makes them ideal for repetitive industrial tasks”
APEM
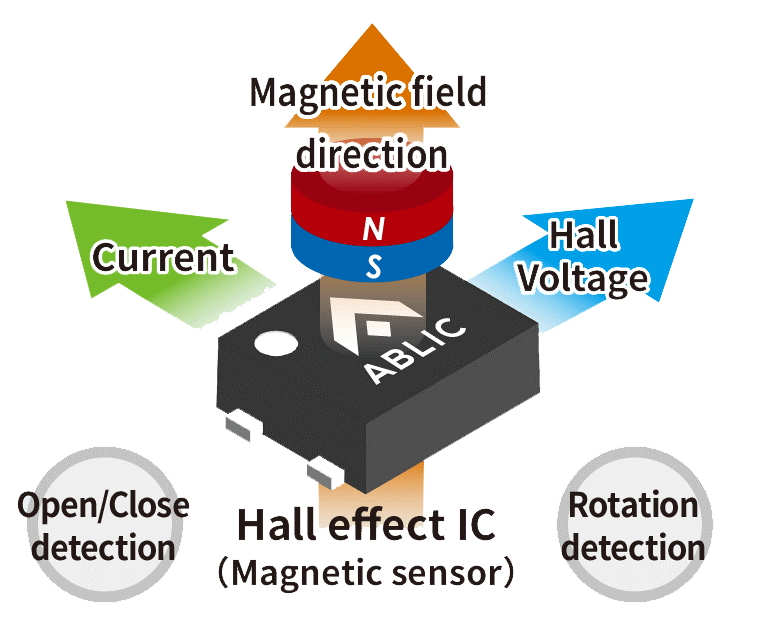
HALL EFFECT SENSORS VS. POTENTIOMETERS: UNDERSTANDING JOYSTICK DISPLACEMENT TECHNOLOGIES
The joystick offering on the market is large and diversified and it is not easy to find the more relevant technology.
For demanding applications, there are two different technologies being used to measure displacement of joysticks.
The first uses potentiometers, variable resistors that create a voltage change in response to movement. Potentiometers represent a tried and trusted technology that has been used for many years in a wide range of controls. However, potentiometers are electromechanical devices that can wear out.
The second technology uses Hall effect sensors. These sensors measure the magnetic field of a magnet to determine its position and movement.
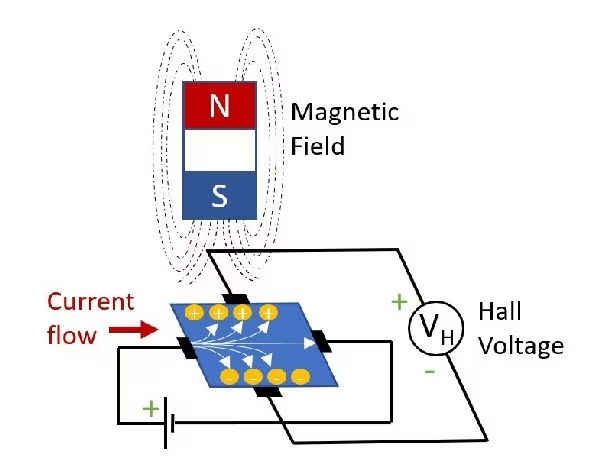
HOW DOES A HALL EFFECT SENSOR WORK?
Hall effect joysticks are proportional: the output voltage varies per the actuator position. Concretely, the movement of a magnet placed beneath the actuator modifies the electromagnetic field when the actuator is operated. An electric sensor placed on a PCB in front of the magnet measures the intensity variation and determines the actuator position precisely.
To sum up, the electromagnetic field created by the magnet movement is calculated by the sensor, which traduces it into an output voltage.
HALL-EFFECT SENSORS’ MAIN ADVANTAGES
LONG LIFE EXPECTANCY
Hall effect is a contactless technology, without any risk of component wear. Joysticks utilizing this technology have a long life expectancy (over 10 million cycles) and are adapted for repetitive industrial applications with a large number of cycles (24h/24h control stations).
FAVORABLE QUALITY/PRICE RATIO
Made of few components, Hall effect joysticks are simple to assemble. Their production requires few mounting stages and reduced labor. They have an excellent quality/price ratio for large volume industrial projects compared to expensive contactless technologies like potentiometric joysticks.
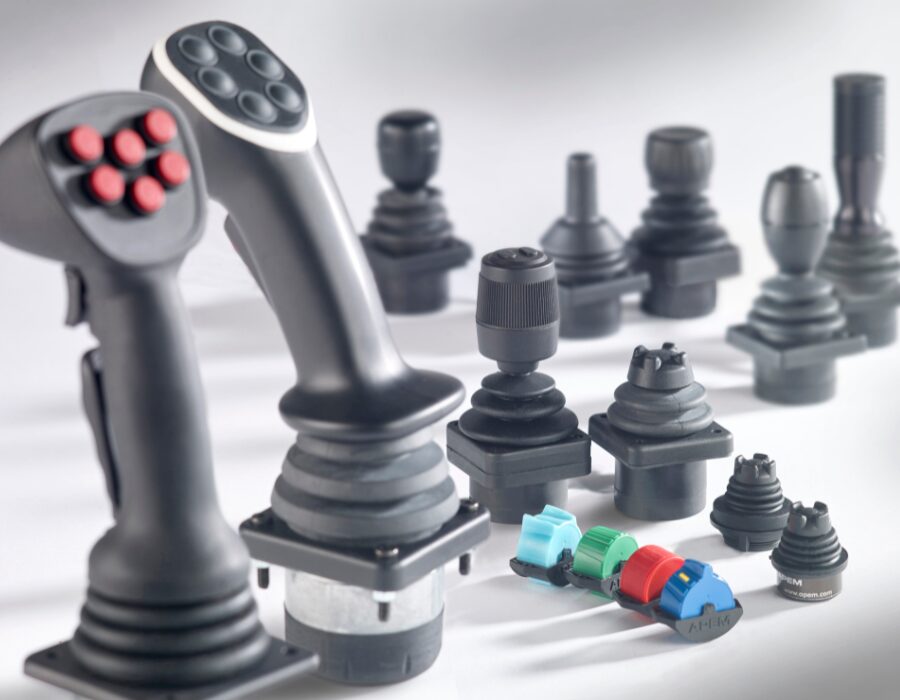

ADAPTED ERGONOMIC DESIGN INCLUDING RESISTANCE TO SHOCK AND VIBRATION
Another advantage of the contactless construction of the Hall effect sensor is that it is more resistant to shock and vibration, making this technology invaluable in high-vibration applications such as industrial vehicles and heavy machinery. Their construction is also low-profile and does not need the depth behind the panel that a conventional potentiometer joystick requires, a significant advantage in today’s cramped vehicle cabs.
INCREASED SAFETY
To increase user safety, APEM has developed a range of “double heart” Hall effect joysticks. These joysticks have redundant output signals. The signal is doubled on independent wires. This system allows to detect any operation error (output voltage outside reference range) and automatically sets the joystick in “off” mode. Hall effect joysticks also have a very good electromagnetic immunity.
DISCOVER APEM’S RANGE OF HALL EFFECT JOYSTICKS
APEM’s handgrip joysticks offer superior durability and precision for off-road and material handling, featuring ergonomic handles for one-handed use and integrated components for efficient multi-function control.
APEM’s mid-size joysticks deliver compact, versatile control for various hand sizes, integrating multiple functions to support electronic proportional control in material handling, construction, and specialty vehicles.